In case of double layer composite material, the low carbon steel composite layer of the substrate should be Babbitt alloy. Through axial and radial positioning, the bearing makes that the pad is fixed onto the substrate. With proper design of profile and high accuracy machining, the pad may be free inclined under dual action of revolution and load, forming oil wedge for dynamic lubrication of bearing. The Babbitt alloy mainly contains tin, lead, copper and antimony. The copper is used to improve the strength and hardness of the alloy of which structural features are that hard phase particles are evenly distributed on the soft phase substrate. The soft phase substrate makes that the alloy features very good inset, adaptability, and resistance to seizure. And, after running in, the soft substrate is concave and hard particles are convex, so that micro clearance is formed between the sliding faces, as an oil storage space and a lubricating oil channel, good to reduction in friction. The concave hard particles function to support, good to bearing capacity.
d (mm) | D (mm) | H (mm) | Number of pads | Load (kN) |
40 | 90 | 45 | 5 | 2 |
50 | 95 | 69 | 5 | 3.5 |
60 | 120 | 82 | 5 | 5.5 |
75 | 140 | 95 | 5 | 8.2 |
90 | 155 | 107 | 5 | 10.5 |
100 | 177 | 120 | 5 | 14.5 |
115 | 190 | 133 | 5 | 18.6 |
125 | 215 | 149 | 5 | 22 |
140 | 228 | 161 | 5 | 25 |
150 | 254 | 174 | 5 | 32 |
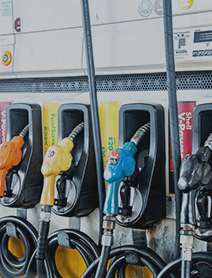
OIL AND GAS
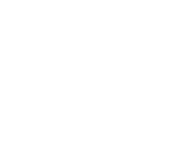