The pad of a tilting pad thrust bearing is made of three layers of composite material including steel substrate, copper layer and composite material. The substrate material is specially treated steel. The composite material of the pad surface is improved PTFE to have lower friction coefficient and better heat resistance. The optimal design of pad structure, special machining process, high accuracy of pad dimensions, and proper thickness of oil film allow that the bearing is easy to dynamically forced lubrication.
PTFE features a range of excellent performances including very low friction coefficient. It is one of self lubricating materials with lowest friction coefficient found at present.
It has high chemical stability and outstanding resistance to chemical corrosion. The operating temperature ranges from -200 to 250°C. It features good resistance to bonding.
In order to improve the friction performance of PTFE material, the PTFE is filled with some filler for modification. The fillers include Cu powder, M0S2, glass fiber, polystyrene resin, Aramid, etc. The modified PTFE is PTFE based composite material, featuring excellent performance of reduced friction and resistance to wear. Compared to pure PTFE, its resistance to wear is higher by 1000 times, creep resistance at normal temperature higher by 1.5 to 4.5 times, heat resistance higher by 1.5 times, hardness increased by 10 to 30 percent, and thermal conductivity increased by 2 times.
D (mm) | D1 (mm) | D2 (mm) | H (mm) | Number of pads | Load (kN) | Maximum speed (r/min) |
65 | 60 | 24 | 28 | 6 | 15 | 4000 |
70 | 65 | 27 | 28 | 6 | 17.5 | 4000 |
75 | 70 | 29 | 28 | 6 | 20 | 4000 |
80 | 75 | 31 | 28 | 6 | 24 | 4000 |
85 | 80 | 33 | 28 | 6 | 27 | 4000 |
90 | 85 | 35 | 28 | 6 | 30 | 3000 |
95 | 90 | 37 | 28 | 6 | 34 | 3000 |
100 | 95 | 39 | 28 | 6 | 39 | 3000 |
105 | 100 | 40 | 28 | 6 | 45 | 3000 |
110 | 105 | 42 | 28 | 6 | 50 | 3000 |
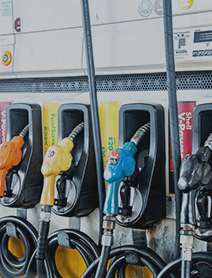
OIL AND GAS
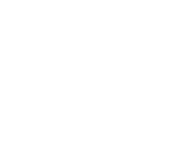