Outer dimension (mm) | Rated Load (KN) | Bearing Model | Weight (kg) | |||||
d | D | B | rmin | r1min | Cor | Cr |
|
|
150 | 210 | 165 | 2.5 | 2 | 945 | 2560 | 382930 | 21.2 |
200 | 310 | 275 | 3 | 2.5 | 2320 | 5880 | 382040 | 75.1 |
300 | 420 | 300 | 4 | 3 | 3175 | 9305 | 382960 | 130 |
400 | 600 | 356 | 5 | 4 | 5635 | 15060 | 381080 | 317 |
480 | 700 | 420 | 6 | 5 | 7400 | 21120 | 381096 | 547 |
500 | 720 | 420 | 6 | 5 | 7550 | 21910 | 3810/500 | 565 |
600 | 800 | 380 | 5 | 4 | 7205 | 23215 | 3819/600 | 536 |
710 | 1030 | 555 | 7.5 | 6 | 13860 | 41215 | 3810/710 | 1568 |
750 | 1090 | 605 | 7.5 | 6 | 15775 | 47485 | 3810/750 | 1874 |
950 | 1360 | 880 | 7.5 | 6 | 26435 | 87060 | 3820/950 | 4087 |
1060 | 1500 | 1000 | 9.5 | 9.5 | 32090 | 109975 | 3820/1060 | 5896 |
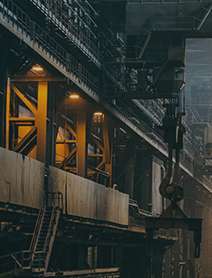
METALLURGY AND CONSTRUCTION
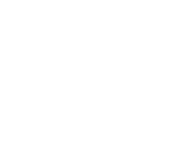